inTime
inTime Delivery in non-hierarchical Manufacturing Networks of Machinery and Equipment Industry
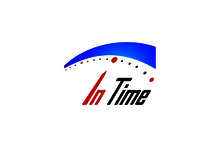
The aim of the research project inTime was to increase the logistic effectiveness and thereby to reduce costs in in non-hierarchical manufacturing networks of machinery and equipment industry.
Non-hierarchical production networks are a common environment for manufacturing companies today. Each company is facing multiple and dynamic relationships within several networks. This complex market situation leads to problems with missing delivery reliability. Delayed supplies lead to wasteful turbulence throughout the entire network. On average a manufacturer has to spend 5.8% of its turnover to compensate the negative effects of delayed deliveries. Besides the stated costs the missing delivery reliability leads to a poor customer satisfaction and increased lead times due to safety stocks balancing delays.
The key objective of inTime was to improve the delivery reliability in each customer-supplier relationship and by that smoothing production in the overall network. To foster delivery reliability each supply had to be rewarded according to the accomplished delivery performance.
inTime should develop an automated trading function to negotiate incentives for delivery reliability. Comparable to an electronic stock exchange the inTime trading function should transform the manual and intransparent negotiation process into an automated and transparent market mechanism. By that a non-centralised coordination within the production networks as it is working similar to the mechanism of the “invisible hand” by Adam Smith should emerge.
Key innovation of the project was to establish a market for delivery reliability. The main research question was whether delivery reliability could be traded trough an electronic market like gold or silver is traded at the metal exchange nowadays.
Besides the development of the market functions, the integration into the entire order process requires several novelties which had to be developed simultaneously. The described negotiation process relied on a highly automated communication between all parties to reduce transaction costs to a minimum. Therefore the previously developed communication platform myOpenFactory was used to exchange standardised information such as prices, quantities, delivery dates, etc. electronically. To automate the entire inTime business process the data model of myOpenFactory had to be expanded. To identify and evaluate the criticality of each supply new functions analysing the internal risk and evaluating the related costs of the ordered parts were necessary. Furthermore, the business partners had to configure their order processes dependent on the customer-supplier relationship and the individual risk. Therefore a configuration method to find the right business process was needed. The achieved improvement in delivery reliability of inTime opens new planning opportunities for companies which had to be realised in the internal planning systems.
The successful developments of inTime were demonstrated and validated by three European wide industry pilots and their non-hierarchical supply networks.
FIR was responsible for both the administration of the workpackage ConceptDesign and the following tasks: Analysis and Concept of a concept to evaluate a reliable delivery with regard to time horizon, uncertainty and risk as well as operative benefits of an in-time delivery
Analysis and development of mechanisms for negotiation of intime delivery. Focus of this task was the negotiation of incentives and penalties in regard to intimacy level and negotiation power in the production network.
Project partners
Topic Area
- Production Management
Research Focus
- Auftragsmanagement
- Produktionsregelung